Environmental Monitoring of Non-Sterile Processes
What is environmental monitoring for medical products & medical devices?
Environmental monitoring is the tools and techniques used to observe an environment, characterize an environment’s quality, and ensure that an environment meets established acceptance criteria. Environmental monitoring for medical products and medical devices covers the acceptance criteria for the environments throughout the entire lifecycle of the product, from raw materials to end-use or expiration. Environmental monitoring is an important quality control metric. It is particularly critical for verifying your medical device or product is devoid of microbes during various phases of manufacturing, packaging, transportation, and storage.
What are non-sterile processes?
Non-sterile processes are methods or procedures that are undertaken in an environment where bioburden is controlled to safety levels based on product attributes, route of administration, and target patient population. Non-sterile processes contrast to aseptic processes, in which the bioburden is essentially eliminated. For a full comparison between aseptic and non-sterile processes, please visit our article HERE.
Why is environmental monitoring for non-sterile processes important for your medical device or product?
Unlike sterile products, microbial content in non-sterile products is controlled to the level needed for patient safety within the parameters of product use. Excessive sterility or aseptic processing controls (such as isolators) add complexity and cost without safety benefits. Eliminating unnecessary sterility or aseptic processing controls saves money for both manufacturers and patients. Non-sterile processing methods may be advantageous to use depending upon your medical product’s end-use. The manufacture of non-sterile products and the management of their microbiological content are distinctly different from those required for sterile products. Sterile products are injected or applied topically to sensitive tissues with a high risk of infection, little to no microbial flora, and no barriers to infection.
In contrast, non-sterile products are administered to regions of the human body that have a high density of natural microbial flora as well as physical and immunological barriers to infection. Even though the microbial requirements for sterile products are stricter, non-sterile products must still go through manufacturing processing that prevents excessive contamination of the product through limiting the microbial chain of infection. Microbial growth in excipients, components, and drug substances is monitored in-depth and is among the most significant causes for concern for non-sterile products. Other common sources of microbial contamination are described HERE. Examples of common non-sterile products are listed below.
The non-sterile pharmaceutical products listed below are ranked with respect to the potential risk of microbiological contamination (from high dry powder inhalants to low risk oral products). The same microbial contamination risk list applies to medical devices for use in the same body areas (i.e., nasopharynx, vagina, skin, rectum, and mouth).
List of common non-sterile pharmaceutical products:
- Metered-dose and dry powder inhalants
- Nasal sprays
- Optics
- Vaginal suppositories
- Topicals
- Rectal suppositories
- Oral liquids (aqueous)
- Liquid-filled capsulesOral tablets and powder-filled capsules
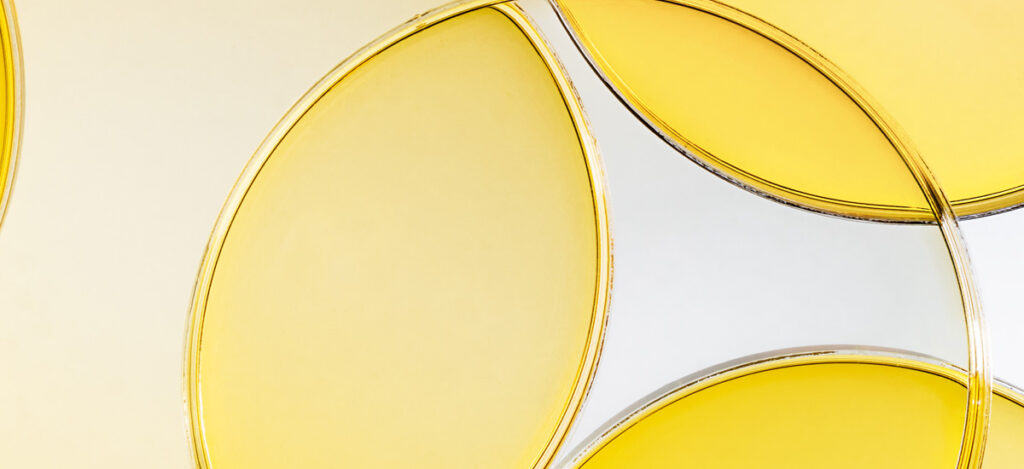
How are manufacturing environments monitored for non-sterile products?
The monitoring of manufacturing environments for microbes is a qualitative tool to minimize contamination risk in non-sterile products. A successful environmental monitoring program confirms the effectiveness of microbiological controls and detects unforeseen contamination issues early, saving time and money. Microbial methods and practices for aseptic facilities may be used but are not intended for non-sterile environments. Often the levels of transient contamination depend on the level of human activity and gowning requirements of the manufacturing facility. This is because most microbial contaminants in clean environments are from humans. In non-sterile products, manufacturers expect controlled bioburden levels that will not risk the end-user. Thus, manufacturers need to establish acceptable levels of microorganisms within each product and perform regular production plant hygiene assessments to keep up the effectiveness of the facility’s microbial environmental controls. Hygiene assessments include microbial sampling, staff evaluation for the appropriate execution of gowning and standard operating procedures, raw material assessments, and evaluations of cleaning protocol effectiveness.
How are manufacturing environments for non-sterile products tested?
Both active and passive air sampling methods are used for the environmental monitoring of non-sterile manufacturing facilities. Active devices sample by air volume and capture viable organisms on solid media plates or strips. Results from active sampling devices are expressed as colony-forming units per unit volume. Passive sampling is performed via settling plates based on time in the manufacturing facility versus air volume sampled. Personnel monitoring for non-sterile product manufacturing is not required. However, personnel monitoring is used if contamination levels exceed set limits. High-traffic areas where materials are transferred into and out of the area are susceptible to transient microbial contamination are areas where microbial sampling is used. In most non-sterile hygienic assessments, characterization of the microorganisms, cellular morphology, Gram reaction, and simple diagnostic testing are used to assess contaminants. Water sampling may also be performed to ensure water for equipment cleaning is suitable. A comparison between water sampling and air sampling methods can be found HERE.
Once a product has been placed into a packaging container, microbial monitoring is not required. Products resistant to microbial colonization or have microbiocidal characteristics need little or no microbiological monitoring for non-sterile manufacturing. Additionally, environments for tablet and powder- and liquid-filled capsule manufacturing need no or infrequent monitoring. The microbial monitoring frequency reflects the potential risk associated with the dosage form. Manufacturing areas for higher-risk dosage forms, such as inhalant products, require more frequent monitoring and typically are manufactured in ISO 8 classified rooms. There are no standardized environmental sampling methods, and monitoring is a qualitative evaluation of general facility hygiene. Thus, a small number of microbial air samples is enough to establish a baseline for a manufacturing environment. Further, general hygienic conditions of the environment should not be used in product-release decisions due to the qualitative nature of environmental monitoring.
The microbiological control of non-sterile products can be enhanced by adopting the following contamination control processes:
- Decontamination of product contact surfaces, materials, and containers, typically by heat treatment
- Chemical or physical (e.g., dry or moist heat) bioburden reduction treatments for raw materials and active ingredients
- Use of closed, cleaned, or decontaminated systems for handling and transfer of materials
- Use of disposable components or utensils
- Improved gowning materials for operational personnel
- Use of ISO classified environments in high-risk operations
The active microbial control measures above can be applied as needed to reduce microbial contamination during the manufacture of non-sterile products.
Summary
Overall, the control of contamination in non-sterile product manufacturing is different from the control of contamination for sterile products. Sterile products are injected or applied topically to sensitive tissues with a high risk of infection, little to no microbial flora, and no barriers to infection. In contrast, non-sterile products are administered to regions of the human body that have a high density of natural microbial flora as well as physical and immunological barriers to infection. Examples of non-sterile products include oral tablets, nasal sprays, topicals, and rectal suppositories. Unlike sterile products, microbial content in non-sterile products is controlled to the level needed for patient safety within the parameters of product use. Eliminating unnecessary sterility or aseptic processing controls saves money for both manufacturers and patients. Environmental sampling is used for both sterile and non-sterile environments. However, in non-sterile environments, a certain level of microbial contamination is acceptable and expected. All in all, whether you need non-sterile or sterile processes for your medical device or product, ensure you choose a contract testing organization that can support you with appropriate and consistent environmental monitoring for manufacturing operations.
Ethide Labs is a contract testing organization that specializes in Sterilization Validations and Environmental Monitoring. Ethide Labs provides in-vitro cytotoxicity tests in-house and outsources in-vivo cytotoxicity work for toxicity testing of medical devices, products, and drugs. Ethide Labs also offers Bioburden Testing, Microbiology Testing, Bacterial Endotoxin Testing, EO Residual Testing, Package Integrity Testing & Cytotoxicity Testing services for medical device companies and allied industries. Ethide is an ISO 13485 certified facility.
References
United States Pharmacopeial Convention. <1115> Bioburden Control of Non-Sterile Drug Substances and Products. Rockville, MD, USA. 2021. (USPC <1115>).
Share this in your social networks