What Are Restricted Access Barrier Systems (RABS)?
What are aseptic, non-aseptic, and sterile manufacturing?
Aseptic manufacturing covers processes, activities, and procedures undertaken in a sterile environment. The sterile manufacturing environment (aseptic environment) is maintained through specialized equipment that prevents microbial material from technicians, raw materials, or machinery from contaminating medical devices or products.
The terms aseptic and sterile are not synonymous, even though product labels utilize sterile and aseptic interchangeably. While both sterile and aseptic manufacturing will prevent microbial contamination following product use, the processes by which microbial contamination is prevented are different. Sterile is a broader term and encompasses microbial contamination prevention through a complete absence of viable microorganisms or the death of microbes that have the potential to reproduce. In contrast, aseptic manufacturing only prevents microbial contamination by ensuring the absence of microbes during processing, not by killing viable microbes.
Thus, sterile products are often manufactured in non-aseptic environments and then chemically or heat sterilized after being filled or placed into their final packaging. The chemical or heat sterilization process ensures that any microorganisms inside the products (obtained during manufacturing and packaging) are no longer viable. In contrast, aseptic manufacturing prevents contamination by the exclusion of microorganisms. For microorganisms to be excluded, an aseptic healthcare product’s manufacturing and packaging processes happen with sterilized materials in a controlled environment designed to prevent microbial contamination of the product.
Products that require aseptic manufacturing are those that often cannot undergo terminal sterilization processes, such as parenteral products and certain implantable devices. Products taken/applied through oral, nasal, or topical routes don’t require aseptic manufacturing.
What are examples of products manufactured in aseptic environments?
- Pharmaceutical sterile products
- Bulk sterile drug substances
- Sterile intermediates
- Excipients
- Medical devices
- Biologics
What are restricted access barrier systems?
Restricted access barrier systems (RABS) are a type of sterile processing environment for non-sterile and sterile manufacturing. RABS are built inside ISO 5-7 clean rooms. They provide ISO 5 unidirectional air inside the barrier and prevent contamination with an air overspill system from within the barrier. Open RABS have specialized barrier openings to enable human intervention. Closed RABS do not allow human intervention and operate with the same operator restrictions as isolators. Closed RABS operate with positive or negative pressure, similar to isolator systems. Sterile items are manipulated in RABS using glove ports. Materials are transferred aseptically without opening the system. A RABS, like other regulated cleanrooms, requires decontamination before use.
What are restricted access barrier system classifications (RABS classifications)?
RABS are classified as open or closed (as described above) and either passive or active systems. A passive RABS does not have its own air filtering, recirculation, or conditioning. Instead, passive RABS air supply comes from the cleanroom it is contained within. In a passive system, cleanroom air flows from the ceiling to the RAB and returns to the surrounding cleanroom through openings under the doors. Closed passive RABS use the cleanroom’s ventilation systems and filter ceiling. In closed passive RABS, air passes through prefilters and ducts into the cleanroom’s air conditioning system instead of returning to the surrounding area.
In contrast, an active RABS has an attached air-handling unit (with a HEPA filter). Fresh air is drawn from the cleanroom, so any air-cooling system connected to the RABS air-handling unit is limited. Active closed RABS always have air-filtration and air-conditioning systems that keep aseptic conditions within the RABS constant. Within active closed RABS, the air is recirculated through ducts after prefiltration.
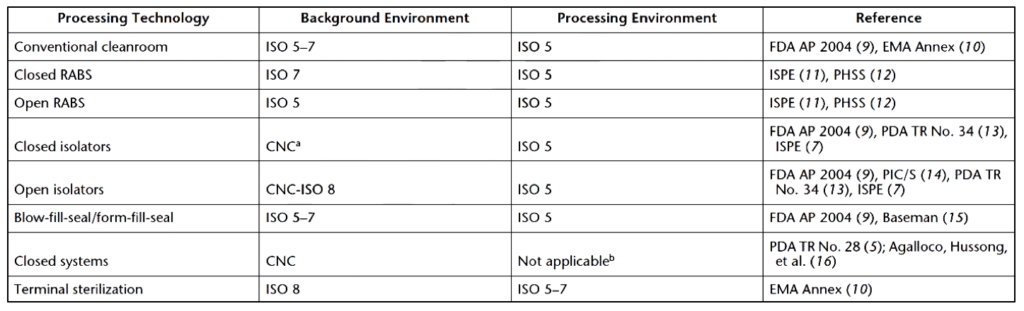
How are restricted access barrier systems designed and operated?
#1: Open RABS Operation
In RABS, incoming air passes through high-efficiency (HEPA Class H14 or better) filters and is evenly distributed by a sterile manifold. Glove ports are the only means of access to products and equipment within the RABS. Thus, aseptic transfer systems are used to move materials and products into and out of the RABS.
Glove Integrity Checks
Glove checks are part of guaranteeing RABS barrier integrity. Before use, gloves are tested for leaks and damage. Physical testing of the gloves before sterilization and mounting occurs in addition to visual glove examinations. Some RABS prefer to test mounted gloves since the entire glove assembly (including the mounting ring) can be verified when the gloves are mounted. However, testing the gloves before mounting can reduce set-up time.
Glove sterilization and installation is the second challenge facing RABS glove integrity. For installation, gloves are pre-sterilized in an autoclave, transferred into the cleanroom, and installed to the mounting ring aseptically. Glove mounting requires experience. Some operators prefer to reverse the mounting ring to aid the glove-mounting process. However, reverse mounting often requires the use of a longer glove.
Sterile Material Transfer Checks
Materials, products, and tools must be transferred in and out of the RABS sterilely. A RABS uses a double-door transfer with steam sterilizers, a transfer chamber, or a simple transfer door to move materials in and out of the barrier. Transfer chambers have interior and outer doors that interlock such that only one door can be opened at any point in time. The interior of the transfer container should be ISO category 5 for RABS. If simple transfer doors are used, they are installed below the RABS process level to reduce the impact of ambient air on the aseptic area. Closed RABS can be operated with positive pressure. However, opening the doors of a closed RABS is not allowed.
Disinfection System Checks
The sanitation of a RABS is complex, as all interior surfaces must be sanitized. Each cleaning with human operators risks contamination and the movement of low-quality outside air into the RABS. Thus, most RABS and all closed RABS have automatic clean-in-place (CIP) systems. CIP systems use steam and other sanitizing agents to clean RABS surfaces and eliminate the need for manual cleaning. CIP and sanitization system functionality is essential to RABS cleanliness for product assembly, filling, or handling.
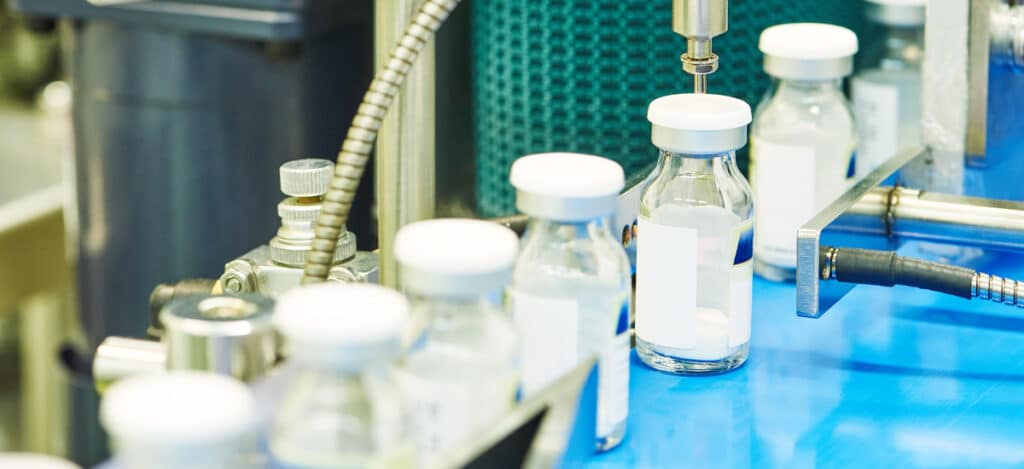
#2: Closed RABS Operation
Closed RABS are special cases because they must meet aseptic and industrial safety requirements. As mentioned earlier, the recirculated air in a closed RABS must be prefiltered before returning to the air-recycling system. Thus, closed RABS must have protocols for contamination-free prefilter changes (i.e., bag-in-bag-out). Pressure-isolation zones and buffers protect upstream and downstream equipment from filling-area contamination. Pressure zones require specialized sealing requirements. RABS operation and design have three primary elements to ensure safe use: glove integrity checks, sterile material transfer checks, and disinfection system checks. Industrial safety requirements and product exposure limits determine the leak tightness of a closed RABS. In cases with peak sealing requirements, the requirements and costs of a RABS are the same as an isolator system.
Summary
Overall, restricted access barrier systems (RABS) are a type of sterile processing environment for non-sterile and sterile manufacturing. The four types of RABS systems are open active, open passive, closed active, and closed passive systems. Sterile items are manipulated in RABS using glove ports, and material transfers occur without opening the system. Closed RABS have special aseptic and industrial safety criteria that must be met. Closed RABS criteria vary depending on the product exposure limits and industrial safety requirements. In some cases, the sealing requirements and costs of a RABS are the same as an isolator system. Many contract manufacturing organizations use RABS systems for their manufacturing and testing processes. When outsourcing regulatory testing, ensure you choose a contract testing organization that can support you with appropriate equipment to test your unique medical devices or products.
Ethide Labs is a contract testing organization that specializes in Sterility Testing and Environmental Monitoring. Ethide Labs also offers Bioburden Testing, Microbiology Testing, Bacterial Endotoxin Testing, Ethylene Oxide Residual Testing, Cytotoxicity Testing & Package Integrity Testing services for medical device companies and allied industries. Ethide is an ISO 13485 certified facility.
References
Michael J. Akers. Sterile Drug Products Formulation, Packaging, Manufacture, and Quality. Drugs and the Pharmaceutical Sciences. Informa Healthcare. 2010.
Johannes Rauschnabel. The Advantages of Restricted-Access Barrier Systems. Pharmaceutical Technology, Volume 31, Issue 3. March 2007.
United States Pharmacopeial Convention. <1211> Sterility Assurance. Rockville, MD, USA. 2021. (USPC <1211>).
Share this in your social networks